Microbatteries that Make Sense
Fitbits, car windows, oil refineries -- the roll call of devices and technologies that rely on ultra-small sensors already numbers in the hundreds of billions.
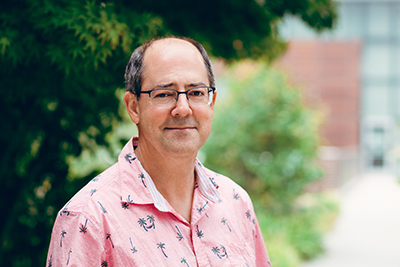
Sensors measure changing conditions and report the data electronically – say, to heat up a bedroom or cool down a nuclear reactor. Sensors with microcircuits are ubiquitous in today’s networks. Some estimates project ten trillion sensors will be in use by 2030.
Ultra-small sensors are powered by their counterparts: ultra-small batteries. As the pace of miniaturization and its applications accelerates, so does the need for ever-smaller sensor batteries that can last a lifetime.
Kristofer Pister, professor of electrical engineering and computer science, leads research to embed microbatteries directly into sensor circuitry, providing a built-in power source instead of an external one. The technology could shrink circuit boards to make the sensor, microprocessor and battery all one unit that can speak to the internet.
The Bakar Fellows Program supports his on-going work to fabricate and print microbatteries within the sensor circuitry itself. Much of the work is also being done by his post-doc, Dr. Anju Toor, who has developed a battery design and fabrication process to print high-capacity batteries. Pister describes the technology and its potential.
Q Besides size, are there other features that make this battery-inside a sensor concept attractive to industry?
A The number one requirement for batteries is connectivity. You have to get the data back to where it needs to go. And you need to do it reliably. The microbatteries we are developing pack a lot of power into a smaller package. They’re also lighter than current batteries and cheaper to produce. Manufacturing them uses the same fabrication and circuit printing technology already used to make trillions of chips.
Q. How are they made?
A The circuitry is stencil printed into cavities on the silicon wafer. You can picture it as etching micro-trenches into the wafer. It’s the same principle as making screen-printed t-shirts. You have a pattern with holes in some areas and not in others. We deposit electrode slurries in the patterned cavities.
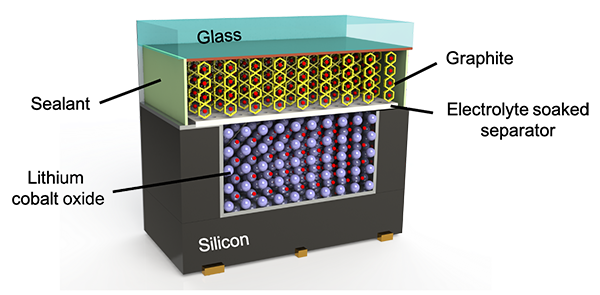
Q How small are the batteries?
A The batteries will be about the thickness of three sheets of paper.
Q It seems that you’re creating something inside the box by thinking outside the box. Why do you think your idea of fabricating batteries directly in the sensor circuits had not been devised before?
A. Many people have made ultra-small batteries because they have seen this need coming. I really don’t know why the idea of embedding the batteries has not been thought of before. It has seemed obvious to me for about ten years.
I founded a company called Dust Networks in 2002. We produced ultra-low power wireless networking chips – we call them smart dust – that could function for a decade on the power of a AA battery. They are now deployed worldwide, from oil refineries to parking meters.
As with all microsensors on the market, I had the battery as separate component, and it was all assembled. But it became clear that to miniaturize the sensors further, the right thing to do is to print the batteries on the wafer.
Q. What part does your Spark award play in this development?
A The Bakar Fellows Program support is about bringing the technology to the point that it can be commercialized. In our collaborations with industry up to now, we have been using micro-batteries off the shelf to power sensors. Built-in power sources would be very useful to support applications from the largest oil refineries to medical devices in clinics and in the home, and for personal health monitoring.
They would work very well for wearables, where comfort and appearance are important. As just one example, they are a natural for applications like smart bandages to monitor wound healing by assessing the healing process of the wound environment. We think this batteries-in-a chip design will be part of devices in the full range of commercial spaces.
The Bakar Fellows Program supports innovative research by early career faculty at UC Berkeley with a special focus on projects that hold commercial promise. For more information, see http://bakarfellows.berkeley.edu.