Putting a new roof over our heads
More than a billion people around the world – hundreds of millions of families – can’t afford secure housing. Researchers project the housing gap will nearly double within a decade.
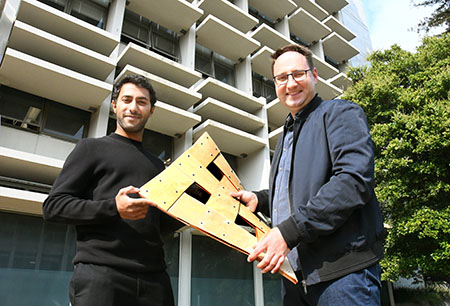
Construction costs looms large in the equation. Simon Schleicher is part of a new generation of architects and engineers developing novel designs and construction technologies to ramp up production of affordable homes. The Bakar Fellows program supports his research to advance the use of 3D printing in home construction.
Layering material to create new structures is already well established in the production of plastic parts with desktop 3D printers. Builders are starting to apply this strategy at a much greater scale to build homes, using concrete as the layered material. But technical hurdles remain.
Schleicher, associate professor of architecture and director of the Design Innovation from Nature research group at Berkeley, describes the potential of 3D printed buildings and his approach to overcome a fundamental construction problem that still limits progress.
Q. To a layperson, 3D-printed homes sounds like more of a fascinating idea than a reality. How far along is this effort?
A. Well, it's certainly a very young field. Countries with a highly developed concrete construction industry are pushing this approach. Here in the U.S., the first 3D-printed house already went on the market in Austin, and the military is very interested in this technology for building barracks.
Q. What are the advantages of 3D printing in construction?
A. It has the potential to make construction faster and cheaper while producing less waste. Concrete is the most affordable and widely used building material in the world. Using one type of material to build the entire structure means you don’t need to coordinate the work of multiple skills -- crews to build the framework and the roof, and others to lay the foundation. You come to the construction site and everything is built with the same machine and is printed in one go.
Q. How is 3D construction with concrete done?
A. The basic principle is the same as 3D printing on a desktop printer, but with concrete instead of plastic, and of course at a much greater scale. This requires large gantry cranes supporting nozzles to extrude the concrete.
Q. What are the limitations?
A. With current methods, you can only build vertical walls -- not wide-spanning horizontal roofs -- because the material is in a liquid state while the structure is built layer by layer. If the print is at an angle rather than vertical, the layers will slump or shift as the concrete is extruded, which can cause the structure to collapse.
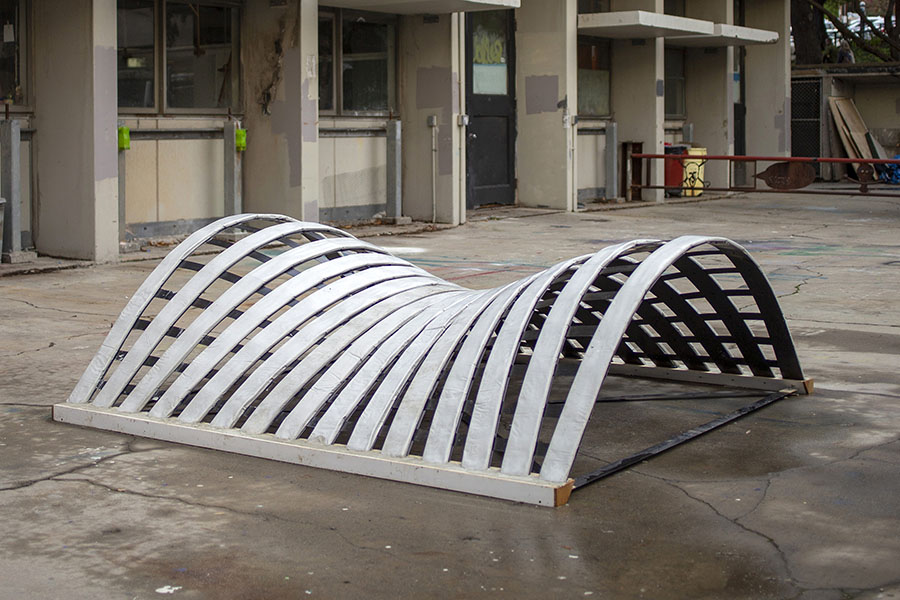
Q. What are you proposing in order to avert the risk of cracking and slumping?
A. We are looking to nature for solutions and have been fascinated by the work of architectural pioneers like Buckminster Fuller and his German counterpart, Frei Otto. They designed buildings which were strongly inspired by shells and spider webs. It is the shape of these doubly curved structures that creates their strength and allows loads to be transferred solely through compression or tension.
The basic principles are by no means new. They have been used in the arches and domes of antiquity. What Fuller and his contemporaries contributed was an unimagined richness of form and deeper understanding of the physics involved.
Q. How does your work build on their findings?
A. I am building a soft, flexible and lightweight formwork, or underlying structure, and applying layers of concrete on top of it. The applied concrete acts like a shell. It gains stability from its geometry, and the ability to withstand force along its 3-dimensional curved shape.
Our tests have shown that the structure is highly resilient. In fact, as soon as you apply the very first layer of material to the formwork, they bond together and strengthen each other. The more layers you apply, the stiffer the structure will become.
Q. Does building this nature-inspired structure require new tools?
A. Yes. 3D printing usually controls the nozzle orientation in three axes. If concrete is extruded along a curved surface with only three axes of nozzle movement, then as the layers build up, spaces will inevitably appear between the layers, compromising its ability to withstand load.
The Bakar Fellows program supports our effort to develop a six-axis robotic printing platform. Here, the nozzle can extrude concrete at the different angles needed to follow the curved contour of the formwork. The robot is mounted on a sliding platform that moves the printhead from one end of the formwork to the other, allowing for significantly longer spans.
The Bakar Fellows support will allow us to build a prototype that spans a full six meters. We think this will show the way to construct a complete building efficiently and affordably.
The Bakar Fellows Program supports innovative research by early career faculty at UC Berkeley with a special focus on projects that hold commercial promise. For more information, see http://bakarfellows.berkeley.edu.