Welcome to the World of Wearable Electronics
An infant born three months prematurely fails to flush pink at birth and has an alarmingly low blood pressure. Ultrasound identifies a heart abnormality and doctors rush the newborn to an MRI suite to confirm the diagnosis. But the scanning itself can cause physical agitation that interferes with clear imaging. In some cases, it can make it harder for the baby to breathe.
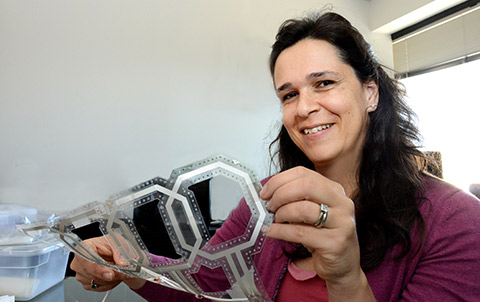
When scans require high sensitivity on a small area of the body, a hard, heavy vest of metal coils must press down on the baby. The bulky burden weighs more than the newborn. Infants squirm under the pressure, but anesthesia to calm them down adds an unwanted risk. Lightening the load by securing the weighty apparatus off the baby leads to degraded resolution, prompting a need for longer MRI exposures.
The hardware is part of the radio frequency (RF) coil assembly that receives the MRI’s electromagnetic signals. Besides being awkward and heavy, the coils are expensive to manufacture and must be reused for years. Sanitizing the bulky assembly is difficult.
Cut to a faculty lunch in 2011. UC Berkeley MRI expert Miki Lustig hears his colleague Ana Claudia Arias describe her lab’s progress adapting a technique similar to conventional ink jet printing to fabricate electronic devices.
It was a technology, Lustig says, that was “well beyond my comfort zone.” But he wondered if Arias’s printable electronics techniques could fabricate ultra-lightweight, “two-dimensional” RF coils to ease the trauma to tiny tots and improve image quality.
Lustig and Arias, both faculty members in the electrical engineering and computer sciences department, walked back to their offices together.
“I asked her if she thought RF coils could be printed. It just seemed like a good idea. She said ‘let me think about it.’ A few days later — almost immediately — she said we should give it a try. She started ordering materials to test different substrates and putting a team together.”
Printing electronic circuits and devices based on metals and semiconductors from solution is a very young field that Arias first entered in 2003 at the near-legendary Xerox PARC in Palo Alto. She came to PARC from Plastic Logic Limited, where she worked after finishing her Ph.D. in physics at the Cavendish Laboratory at Cambridge University, UK.
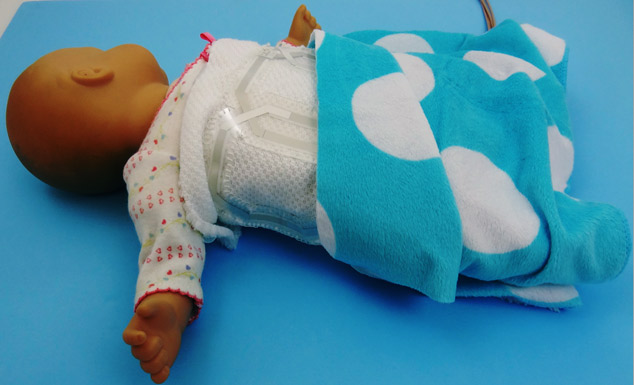
While at Xerox, Arias began to explore fabrication of wearable sensors. Her group developed several components of a flexible sensor that targeted the prevention of brain injuries by monitoring pressure, acoustic and light levels in the battlefield.
When she joined the Berkeley EECS faculty in 2011, she began to expand her collaborations to developed wearable medical devices that could track vital signs and give doctors feedback on their patients health.
“Printed electronics is an ideal technology for fabrication and integration of devices with different functionality, such as sensors, light sources and simple circuits. It is ideal for deposition of unique and customized designs. And when one adds flexible substrates to the equation you could start thinking about truly wearable — and comfortable — electronics”
To make “wearable electronics” for infant MRI patients, her team first tried to print directly onto cloth fabric.
“We wanted to make our coil feel like a swaddle blankie that fits snugly and softly around the babies,” she says.
But the cloth’s texture interfered with the ability to print high quality capacitors, so the team turned to printing the “electronic inks” layer by layer onto plastic thin film, like what is used in photo transparencies. The lab succeeded in fabricating and demonstrating functioning RF coils with performance properties comparable to conventional RF coils.
Arias is supported by a Bakar Fellowship at Berkeley, support intended to help commercially promising research make the leap from the lab to the real world. She and Lustig plan to start a company to advance the technology into clinical use.
“We, researchers, don’t usually have experience and training with steps such as securing IP protection and developing a business plan to attract investment and ensure success. Mentors we met through the Bakar Program have been very helpful,” she says.
Their proof-in-principle of the flexible, lightweight and wearable electronics strategy has led to plans for clinical trials early next year. She and Lustig are collaborating with pediatrician Shreyas Vasanawala at Lucile Packard Children’s hospital to test the wearable RF coils on babies needing MRI scans. Vasanawala has been a key clinical consultant to the project from the beginning.
Arias sees the technology’s potential for adult MRI scanning as well — helping to make the MRI experience more confortable and less scary to everyone, while getting better images of parts of the body that the bulky conventional RF coil assemblies don’t fit very well.
Meanwhile, she still has her eyes on developing that electronic blankie. “When you see kids in the hospital, it’s scary for them. When they’re in a blanket, it’s a much more comforting experience. We want to swaddle them.”