Copper Catalyst Yields High Efficiency CO2-to-Fuels Conversion
Scientists at the Department of Energy’s Lawrence Berkeley National Laboratory (Berkeley Lab) have developed a new electrocatalyst that can directly convert carbon dioxide into multicarbon fuels and alcohols using record-low inputs of energy. The work is the latest in a round of studies coming out of Berkeley Lab tackling the challenge of creating a clean chemical manufacturing system that can put carbon dioxide to good use.
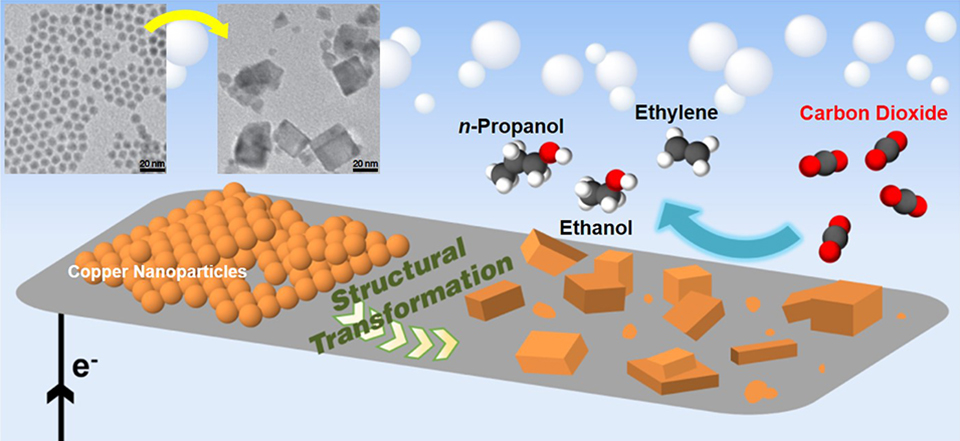
In the new study, published this week in the Proceedings of the National Academy of Sciences, a team led by Berkeley Lab scientist Peidong Yang discovered that an electrocatalyst made up of copper nanoparticles provided the conditions necessary to break down carbon dioxide to form ethylene, ethanol, and propanol.
All those products contain two to three carbon atoms, and all are considered high-value products in modern life. Ethylene is the basic ingredient used to make plastic films and bottles as well as polyvinyl chloride (PVC) pipes. Ethanol, commonly made from biomass, has already established its place as a biofuel additive for gasoline. While propanol is a very effective fuel, it is currently too costly to manufacture to be used for that purpose.
To gauge the energy efficiency of the catalyst, scientists consider the thermodynamic potential of products – the amount of energy that can be gained in an electrochemical reaction – and the amount of extra voltage needed above that thermodynamic potential to drive the reaction at sufficient reaction rates. That extra voltage is called the overpotential; the lower the overpotential, the more efficient the catalyst.
“It is now quite common in this field to make catalysts that can produce multicarbon products from CO2, but those processes typically operate at high overpotentials of 1 volt to attain appreciable amounts,” said Yang, a senior faculty scientist at Berkeley Lab’s Materials Sciences Division. “What we are reporting here is much more challenging. We discovered a catalyst for carbon dioxide reduction operating at high current density with a record low overpotential that is about 300 millivolts less than typical electrocatalysts.”
Cube-like copper
The researchers characterized the electrocatalyst at Berkeley Lab’s Molecular Foundry using a combination of X-ray photoelectron spectroscopy, transmission electron microscopy, and scanning electron microscopy.
The catalyst consisted of tightly packed copper spheres, each about 7 nanometers in diameter, layered on top of carbon paper in a densely packed manner. The researchers found that during the very early period of electrolysis, clusters of nanoparticles fused and transformed into cube-like nanostructures. The cube-like shapes ranged in size from 10 to 40 nanometers.
“It is after this transition that the reactions to form multicarbon products are occurring,” said study lead author Dohyung Kim, a graduate student in Berkeley Lab’s Chemical Sciences Division and at UC Berkeley’s Department of Materials Science and Engineering. “We tried to start off with pre-formed nanoscale copper cubes, but that did not yield significant amounts of multicarbon products. It is this real-time structural change from copper nanospheres to the cube-like structures that is facilitating the formation of multicarbon hydrocarbons and oxygenates.”
Exactly how that is happening is still unclear, said Yang, who is also a professor at UC Berkeley’s Department of Materials Science and Engineering.
“What we know is that this unique structure provides a beneficial chemical environment for CO2 conversion to multicarbon products,” he said. “The cube-like shapes and associated interface may be providing an ideal meeting place where the carbon dioxide, water, and electrons can come together.”
Many paths in the CO2-to-fuel journey
This latest study exemplifies how carbon dioxide reduction has become an increasingly active area in energy research over the past several years. Instead of harnessing the sun’s energy to convert carbon dioxide into plant food, artificial photosynthesis seeks to use the same starting ingredients to produce chemical precursors commonly used in synthetic products as well as fuels like ethanol.
Researchers at Berkeley Lab have taken on various aspects of this challenge, such as controlling the product that comes out of the catalytic reactions. For instance, in 2016, a hybrid semiconductor-bacteria system was developed for the production of acetate from CO2 and sunlight. Earlier this year, another research team used a photocatalyst to convert carbon dioxide almost exclusively to carbon monoxide. More recently, a new catalyst was reported for the effective production of synthesis gas mixtures, or syngas.
Researchers have also worked on increasing the energy efficiency of carbon dioxide reduction so that systems can be scaled up for industrial use.
A recent paper led by Berkeley Lab researchers at the Joint Center for Artificial Photosynthesisleverages fundamental science to show how optimizing each component of an entire system can accomplish the goal of solar-powered fuel production with impressive rates of energy efficiency.
This new PNAS study focuses on the efficiency of the catalyst rather than an entire system, but the researchers point out that the catalyst can be hooked up to a variety of renewable energy sources, including solar cells.
“By utilizing values already established for other components, such as commercial solar cells and electrolyzers, we project electricity-to-product and solar-to-product energy efficiencies up to 24.1 and 4.3 percent for two-to-three carbon products, respectively,” said Kim.
Kim estimates that if this catalyst were incorporated into an electrolyzer as part of a solar fuel system, a material only 10 square centimeters could produce about 1.3 grams of ethylene, 0.8 grams of ethanol, and 0.2 grams of propanol a day.
“With continued improvements in individual components of a solar fuel system, those numbers should keep improving over time,” he said.
The work was conducted through Berkeley Lab’s Catalysis Research Program, funded by DOE’s Office of Science. The Molecular Foundry is a DOE Office of Science User Facility.