Engineering to Restore Power to the People
She’s a whiz at crossword puzzles, but she can’t feed herself. Frustration can turn to fury when muscles and joints weakened by age or a stroke can’t do their job.
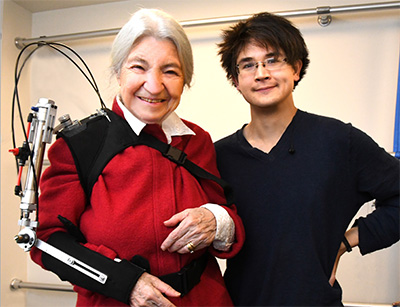
Rehab therapy can often help restore independence. But what if a doctor could just fill out a prescription to boost your strength or range of motion?
Miniaturization and new materials, along with refined engineering, are ushering in a generation of gear that is literally empowering. The military funds development of full-body exoskeletons for super soldiers. At the other end of the spectrum, much lighter-weight wearable devices can assist everyday movements that make for an independent life.
To provide maximum assistance with minimal hardware, the assistive devices must be designed to meet each individual’s specific size, strength and range of motion, says mechanical engineering postdoc Robert Matthew. And that requires a close understanding of how bodies move.
Supported by the Signature’s Innovation Fellows Program, Matthew and Professor Ruzena Bajscy are measuring upper body mechanics in volunteers and developing rigorous mathematical models of the movement. They expect this will provide a foundation to determine the precise assistance people need to restore their ability to carry out daily tasks.
Armed with the new data, they are developing super-lightweight upper body exoskeletons and, with volunteers wearing the devices and performing different tasks, testing the mathematical models’ ability to predict the exact type and degree of assistance needed.
The wearable exoskeletons are intended to provide just enough help to supplement a person’s capacity, and still allow the person to use all the natural strength and mobility they have.
“We need to determine what is absolutely needed to restore the movement or strength and design as simple a device as possible to accomplish those actions — a kind of prescription tailor made for each person,” Matthew says.
“You want to reduce the system down to what is needed and trim the rest away so that people can use their own strength as much as possible. We might measure which parts of your joints are weak, and compensate only for those. It could be just the elbow on one arm.”
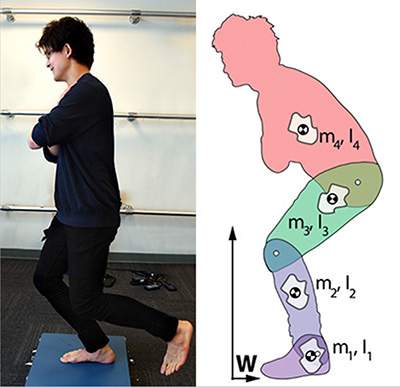
With the Signatures support, Matthew and Bajcsy have developed mathematical models of the body, allowing for measurement of upper and lower limb movement, and providing the foundation for wearable assistive devices to serve a range of physical limitations.
“We’re measuring everything we get our hands on — how far you can reach, how much you can lift, how fast, Matthew says. We want to be able to measure a person’s limits today and predict what they could do tomorrow with some form of assistance.”
In their basement lab in Sutarja Dai Hall, they have been guiding teams of undergraduate engineering students, measuring and modeling joint angles, torque, range of motion, arm length, mass and strength that enable a person to perform daily tasks.
The team then fabricates the lightweight exoskeletons and straps them onto volunteers to test their effectiveness. Early testing allows for refinement of the models, devices, and controllers.
Along one wall in the lab, an upper body design on a mannequin torso does look stripped down, as Matthew says. A cloth vest and straps support pneumatic cylinders about three-fourths of an inch wide that run along the upper arm and forearm. One connects to a mechanical joint near the shoulder; the other joins a similar joint at the elbow.
Joint and arm supports are pneumatically driven. When needed, compressed air stored in a finger-sized cartridge changes the pressure in the exoskeleton to power the supportive exoskeleton. The whole apparatus weighs about as much as a typical laptop. Based on the initial work, Matthew expects the small cartridge to power the device for a full day.
The team has a patent under review for the pneumatic “actuators.” Another patent is in the works for the algorithms they have developed — the mathematical core of the modeling work.
“We expect this new technology will provide needed help in the real world, and the Signatures Fellows Program will help us to get there,” Bajcsy says. “For now, testing is critical. When you make something for people with injuries it takes much more testing of the design — because it could hurt people.
“Our goal is to make these assistive devices as lightweight and inexpensive as possible,” she says. “We can fabricate them using commercially available parts, and with 3-D printing, we expect the devices can be custom-made, with a target cost for individual devices at about $2,500.”
They are currently collaborating with physiotherapists and neuromuscular specialists at UCSF to test the assistive devices on volunteer patients, and also plan to develop the exoskeletons for sports enthusiasts with physical disabilities.
____________________________
The Signatures Innovation Fellows Program supports innovative research by UC Berkeley faculty and researchers in the data science and software areas with a special focus on projects that hold commercial promise.
For more information, see http://live-vcro-d8.pantheon.berkeley.edu/signatures/about.